
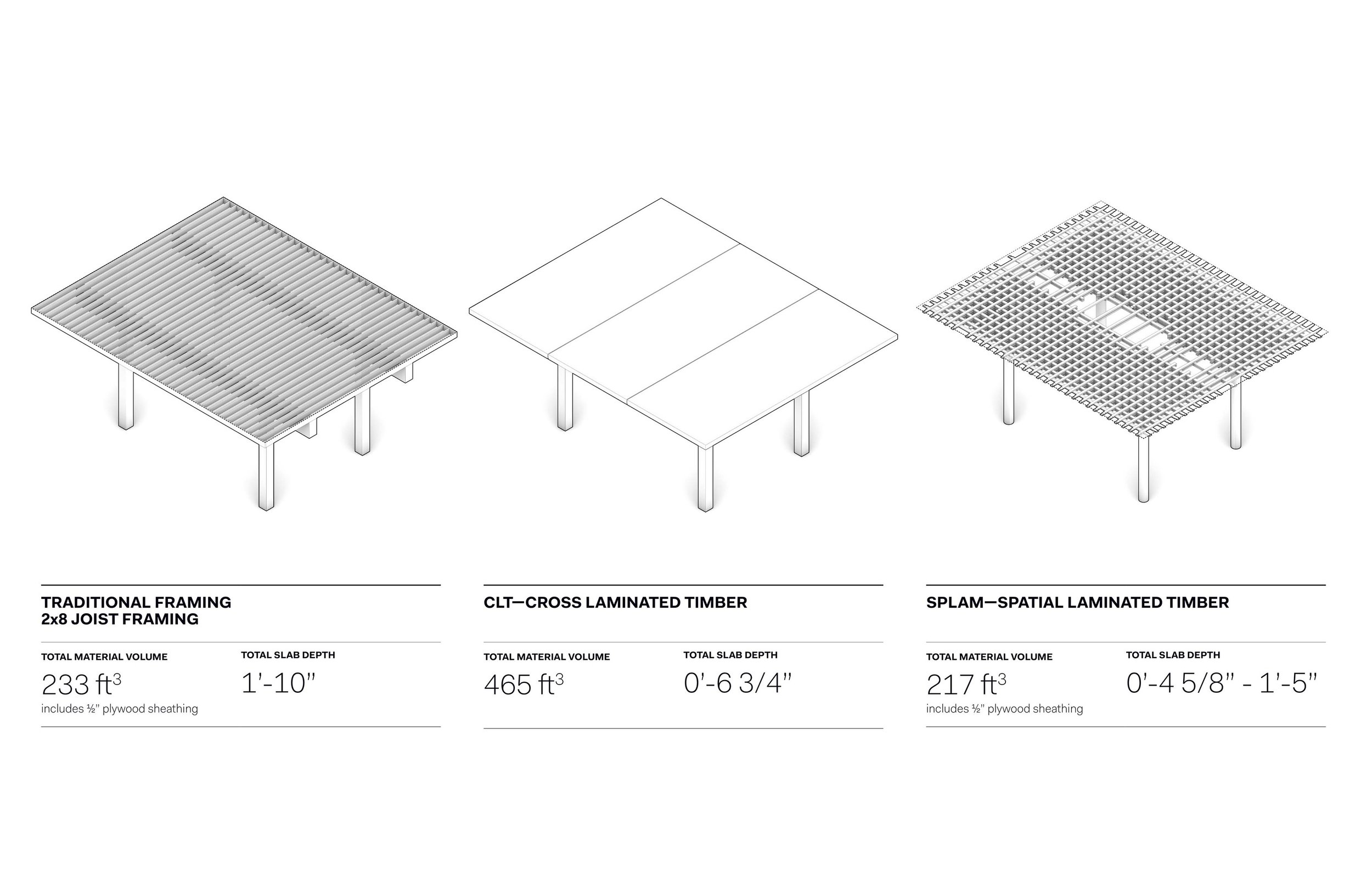
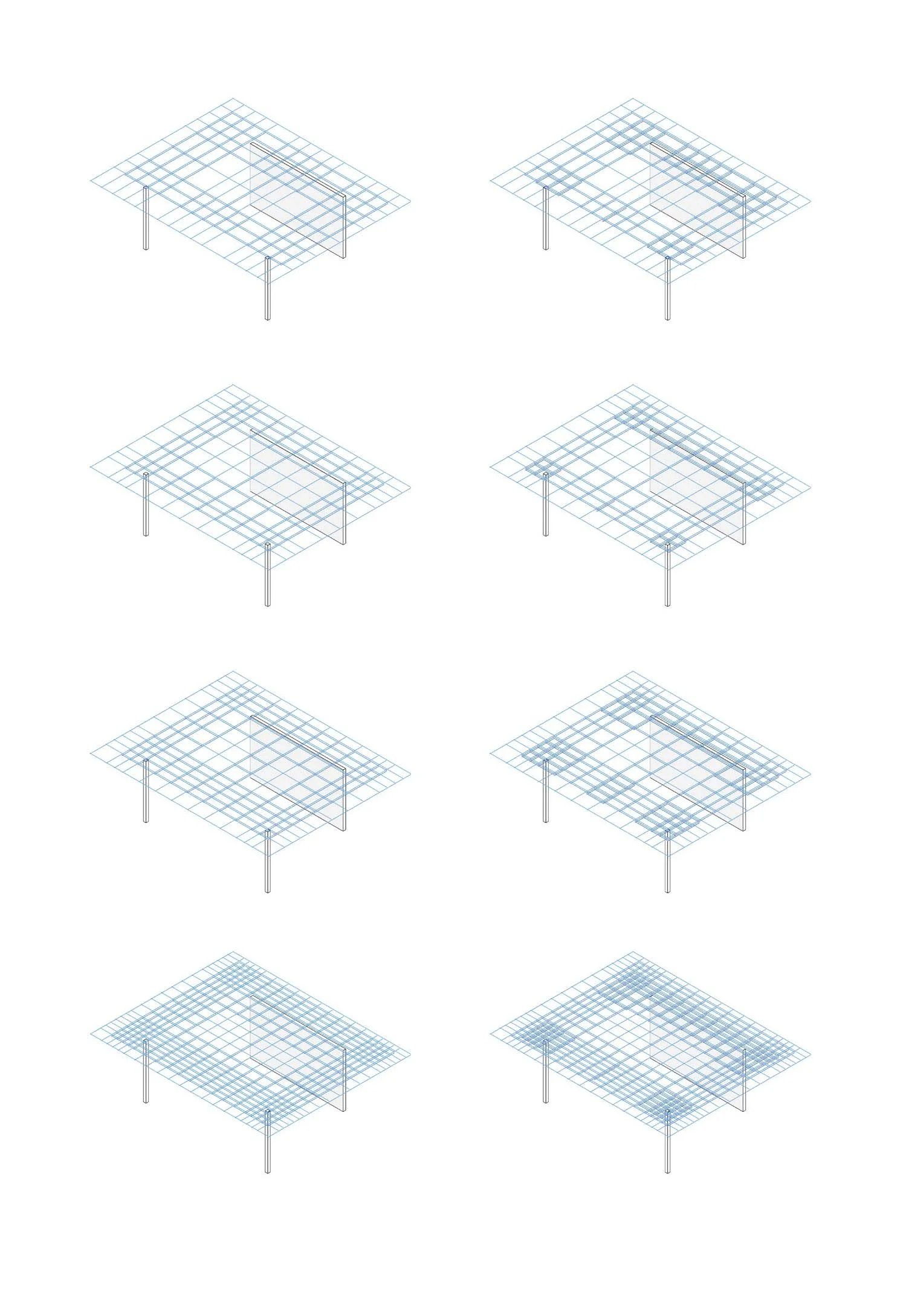
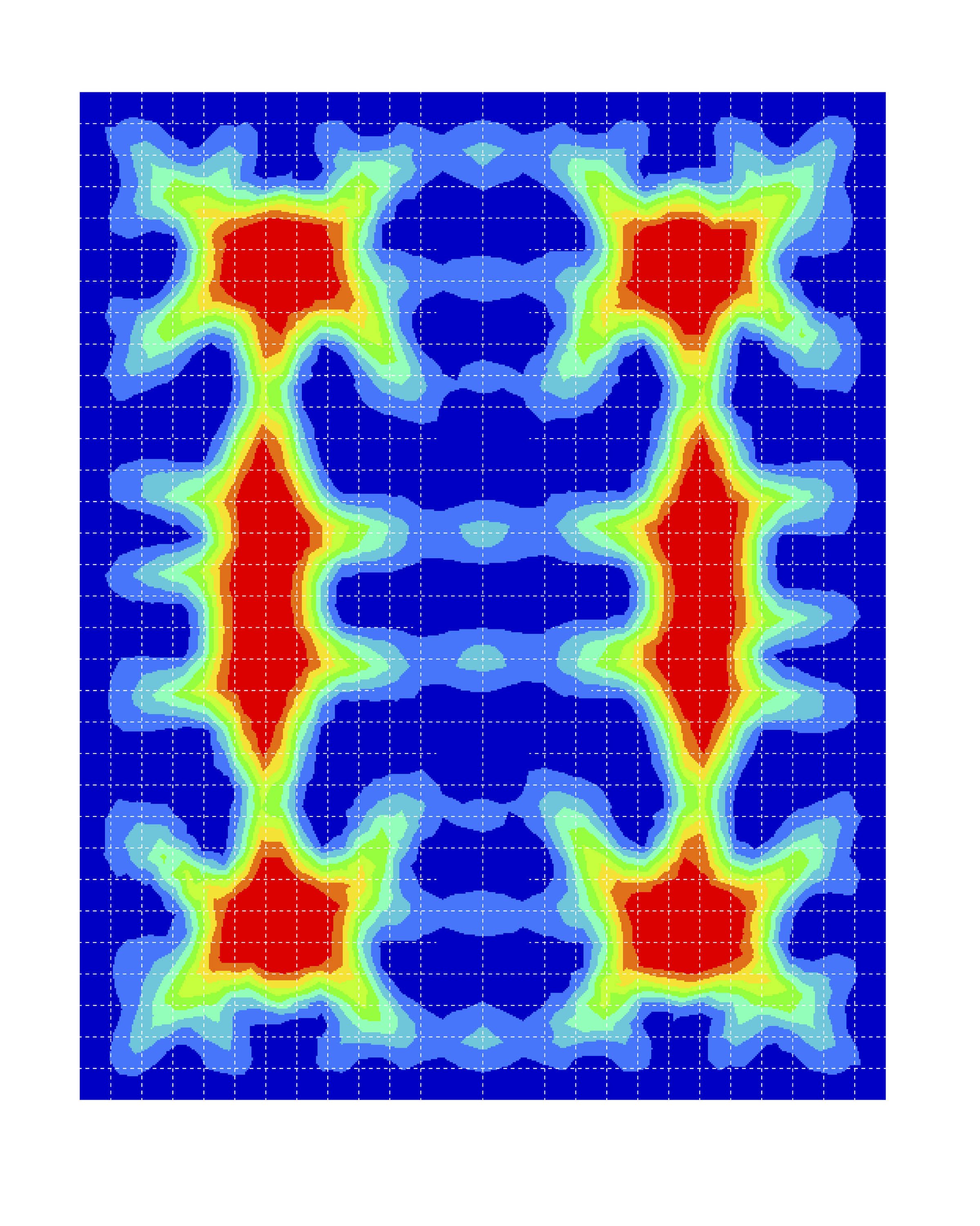
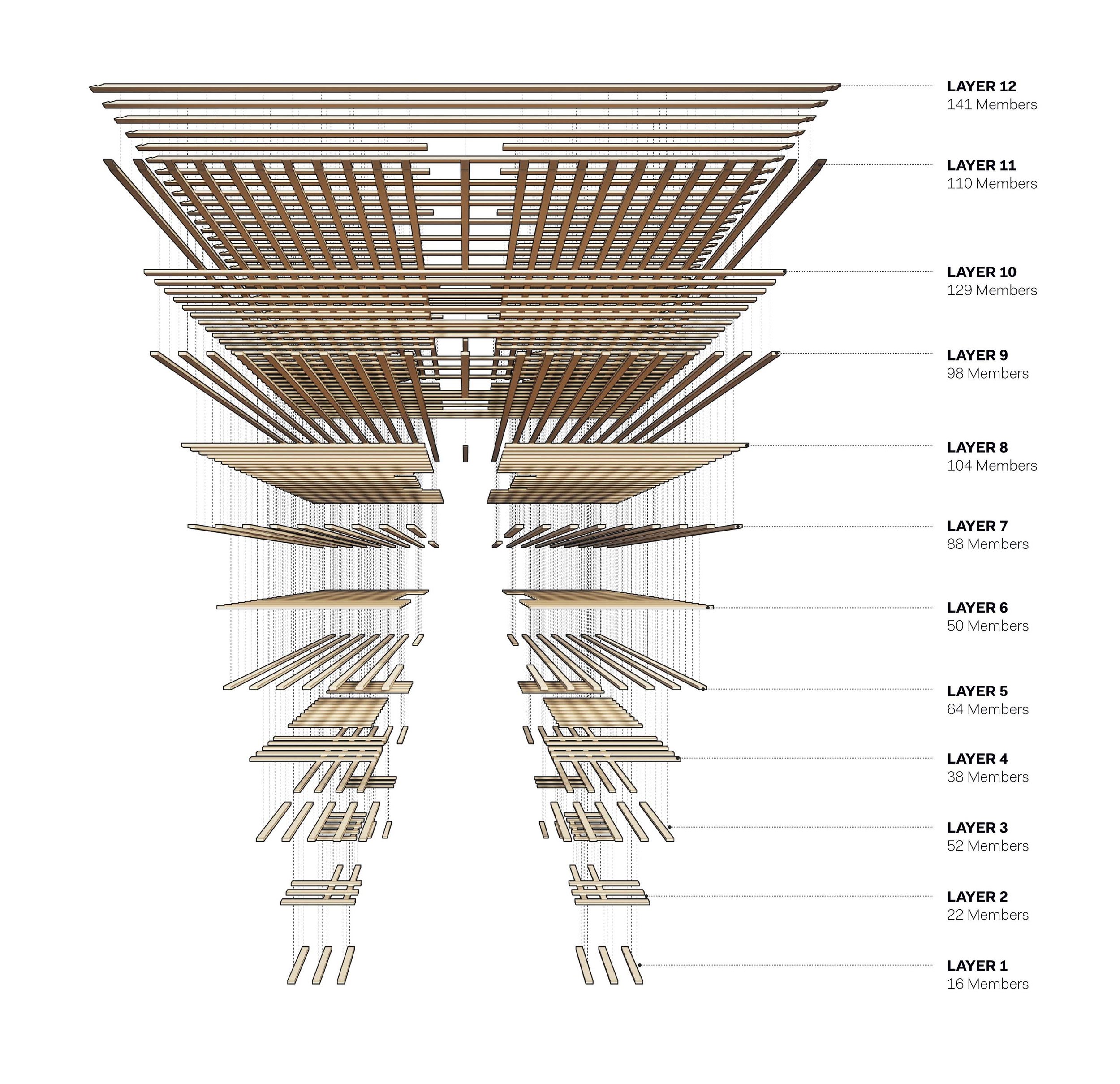

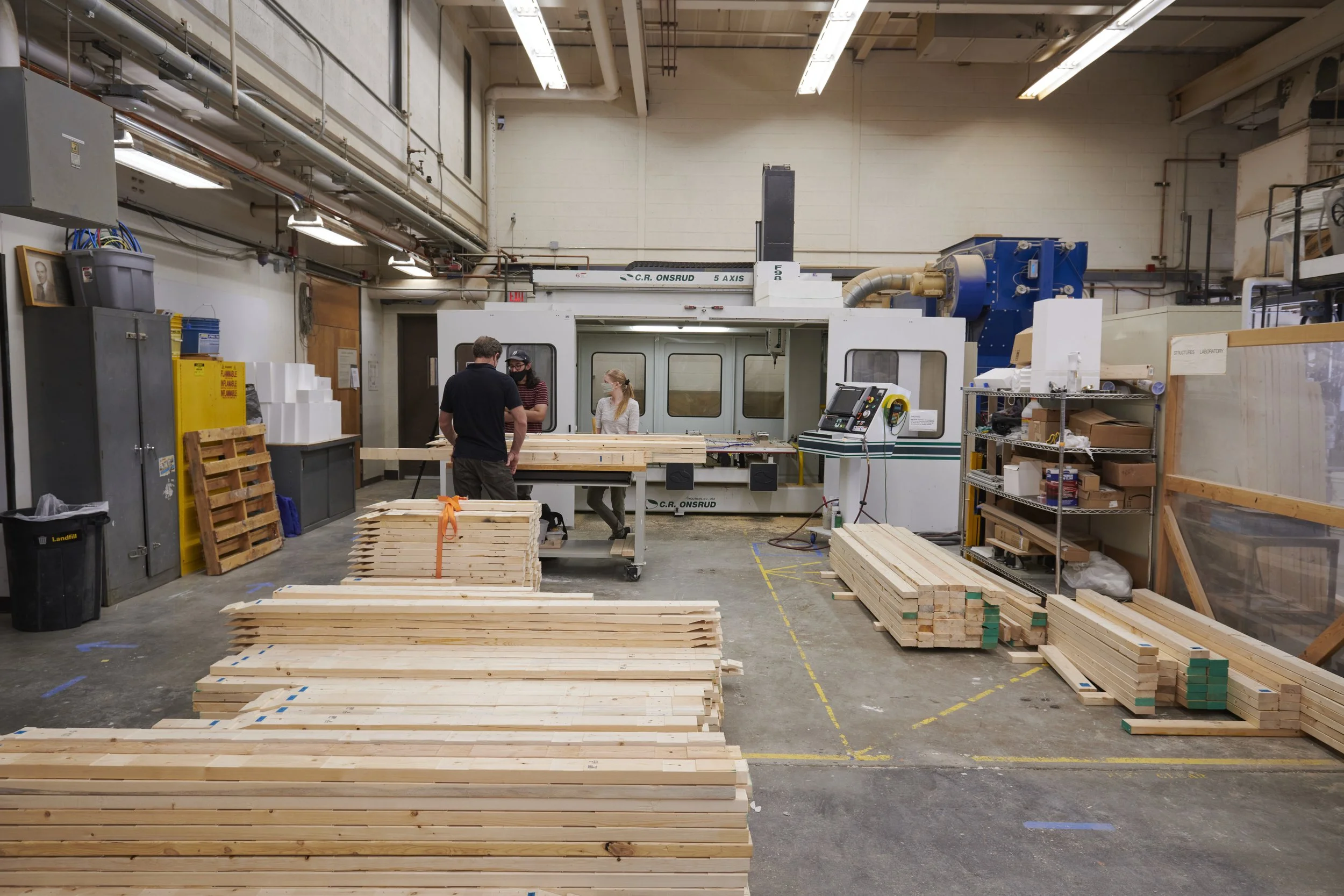
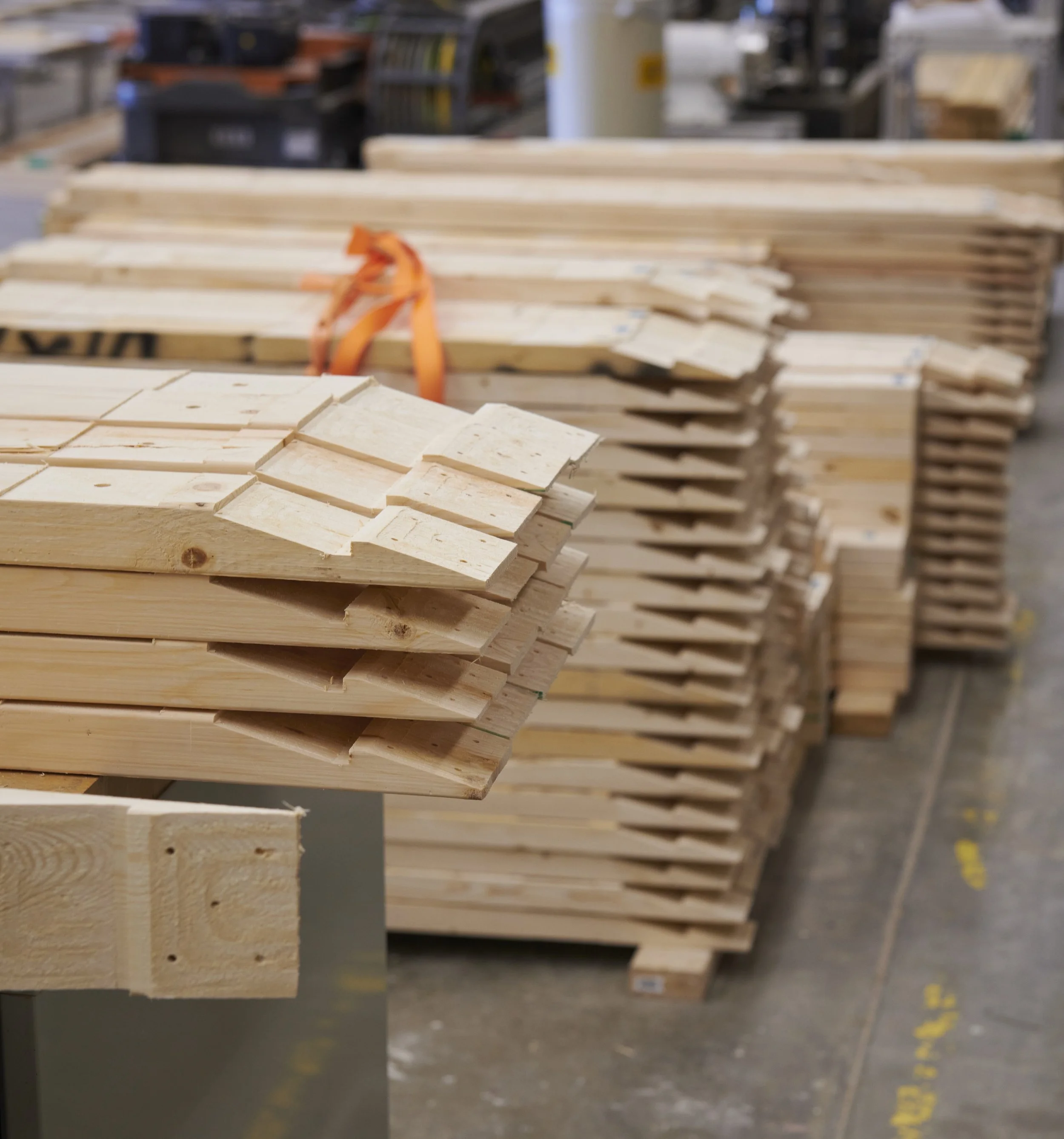
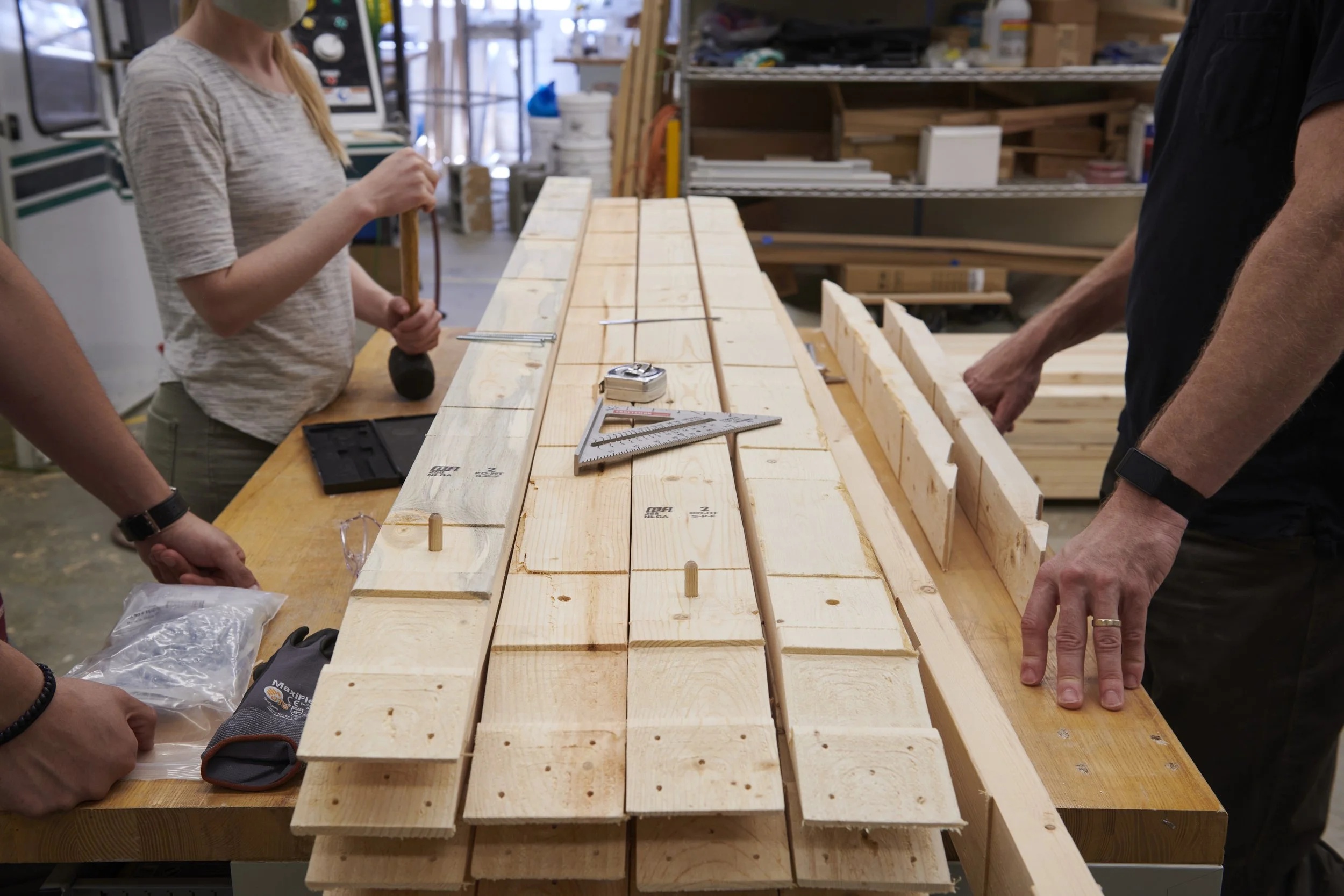






Tsz Yan Ng, Wes McGee, Skidmore Owings & Merrill, & Epic Academy
Date completed: September 2021
Venue/location: 2021 Chicago Architecture Biennial, The Available City, South Shore Chicago, IL
SPLAM, SPatial-LAMinated timber (SLT) reconsiders the conventional use of nominal framing systems, mainly with 2X4s, to design an engineered structure that uses about 46% less material compared to typical Cross Laminated Timber (CLT) structures of the same loading capacity. The SPLAM timber pavilion is a demonstration of this system, as part of the 2021 Chicago Architecture Biennial Exhibition The Available City. The project is a collaboration with Skidmore Owings & Merrill (SOM) and Epic Academy, where the project will remain after the exhibition as a flexible outdoor classroom for the South Shore public high school.
The collaboration focuses on timber as a renewal resource with a low carbon footprint. Instead of mass timber, the choice of using 2X4s highlights the opportunity to use shorter growth pine trees that are more rapidly renewable then larger solid sawn species (translating to lower carbon-footprint) and expands the typical use of 2X4s beyond framing for single-family homes. 2X4s are ubiquitously used as nominal-sized members for construction, especially for wall construction. The shift in use as a slab presents opportunities for continuous extension and the thickness could be tuned for specific applications. Structural topology optimization allows for the design to place members only where it is needed relative to the loading paths. Slab thickness is reduced from 22 inches to 17 inches compared to traditional framing structures, enabling higher floor-to-ceiling heights or for multi-level structures, can translate to an extra floor. Services could also be strung through the openings in the slab, enabling the slab to house all the necessary services without the addition of conduits and ductwork, gaining floor-to-ceiling height for inhabitation. For the Epic Academy pavilion, the slab includes a polycarbonate roof layer at the top for weather protection.
Leveraging advanced milling fabrication processes for the 2X4s, traditional joinery methods such as scarf joints, previously reserved for mass timber construction, are now extended to smaller dimensional members. This enables material efficiency by being able to string shorter off-cuts that might have been previously considered as waste into usable elements for the SPLAM system. The project employs only two joint types, the scarf joint for end-to-end connection, and an overlap joint for cross-orientation layering for sectional thickness. Numerous jointing relations were considered, from doweled and screwed connections, to
The simplicity of the system enabled pre-fabrication and some preassembly of all 912 members off-site with a one-week on-site assembly by a three to four-person crew. To account for inconsistency of 2X4s, a self-centering pneumatic gripping jig was developed to aid the milling process. Physical stress-testing (tension and loading) of joint prototypes provided the data necessary for the engineered system.
Credits:
Design & Engineering Team
Taubman College: Tsz Yan Ng, Wes Mcgee
SOM: Scott Duncan, Adam Semel, Ryan Culligan, Benton Johnson, Kyle Vansice, Rahul Attraya, Rishabh Moorgani, Jonathan Baranowski, Megan Mohney, Sydney Brown, & Chris Whelan
Research Assistants:
Nicolas Garcia, Kaylee Tucker, Hannah Kirkpatrick, Nicholas Di Donato
Fabrication Assistants:
Ellis Willis-Begley, Nick Anello
Funding Credits:
SPLAM was generously supported by Skidmore Owings & Merrill, Autodesk, McHugh Construction, Gremley & Biedermann, and REX Engineering Group