
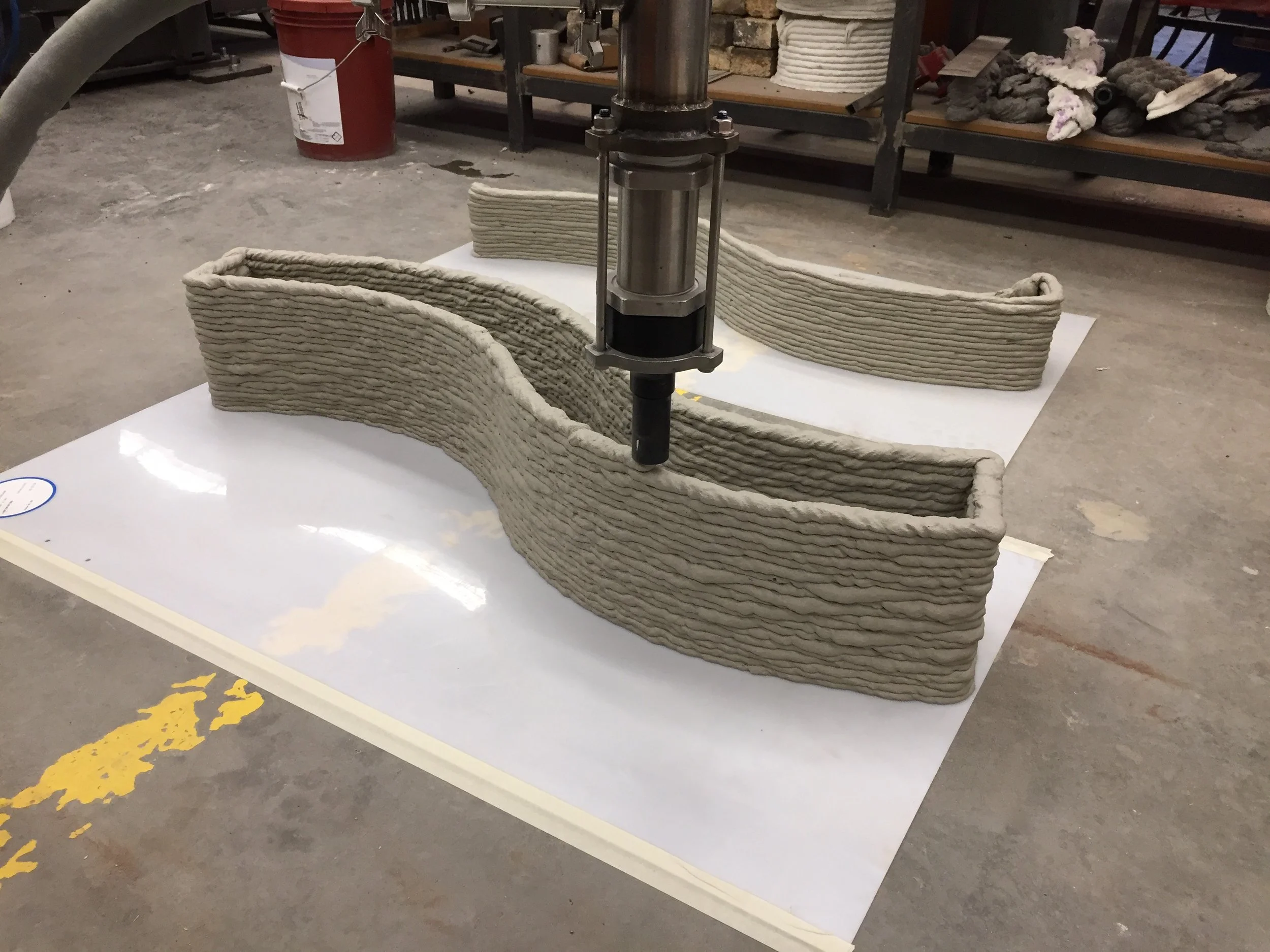


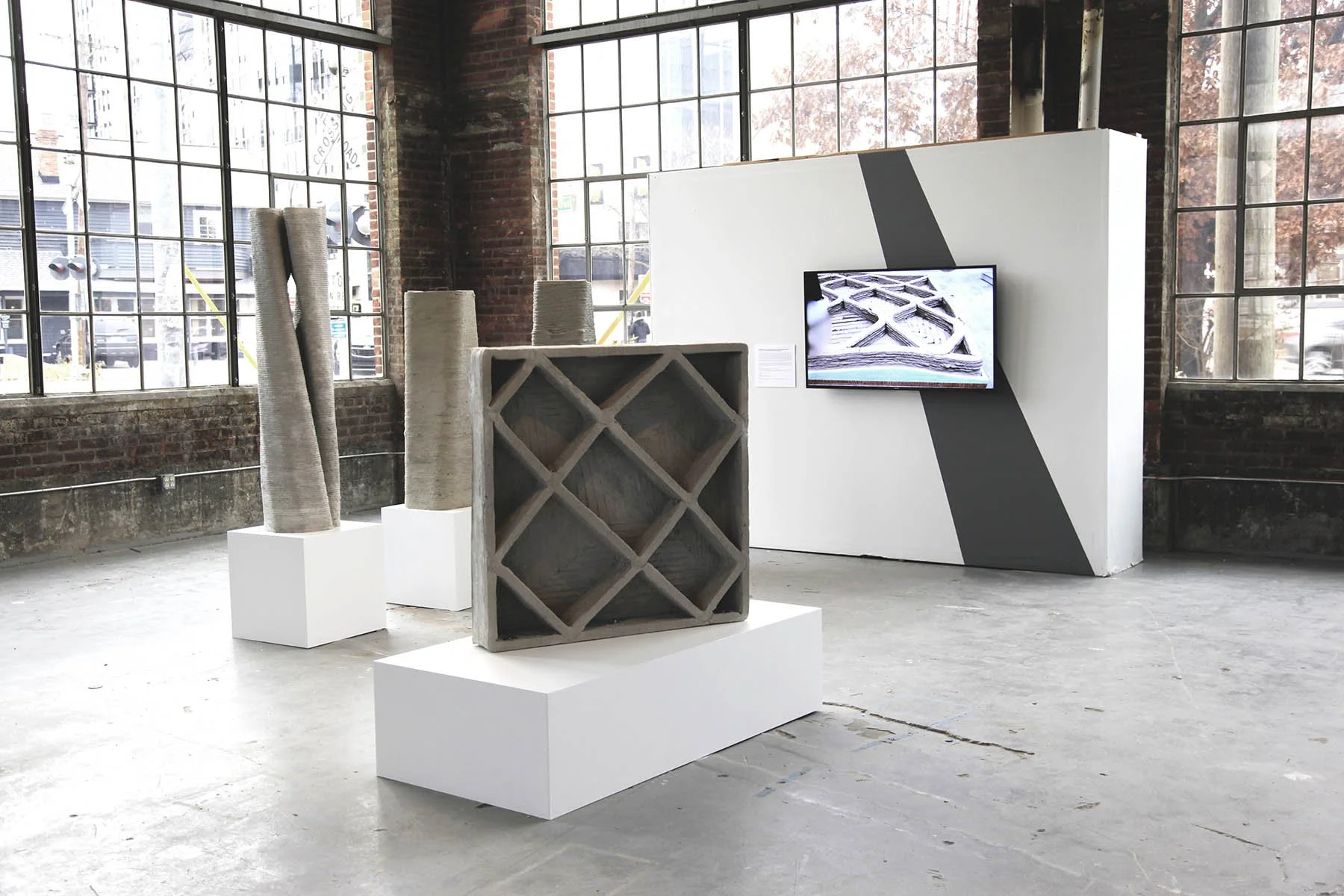


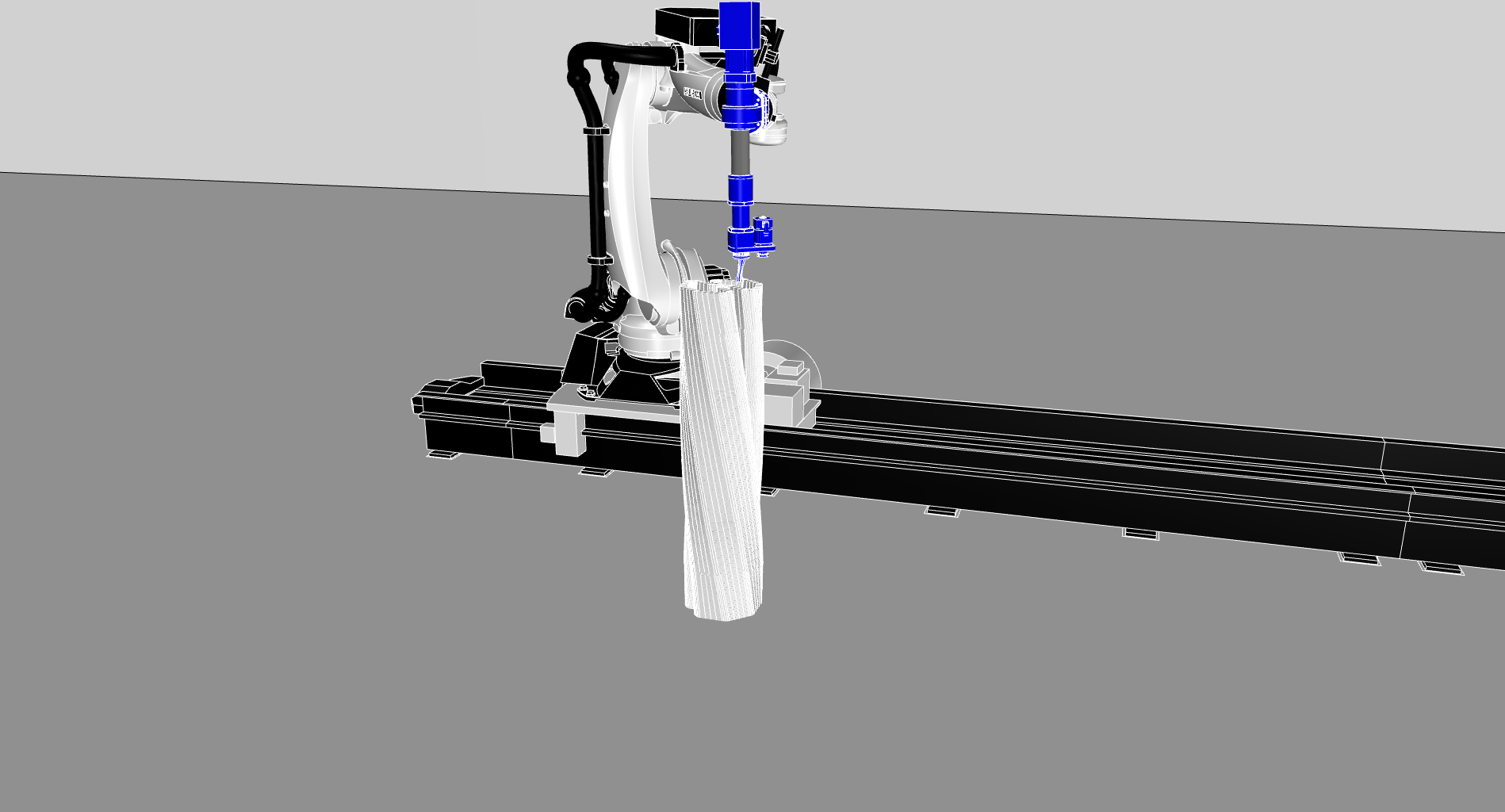


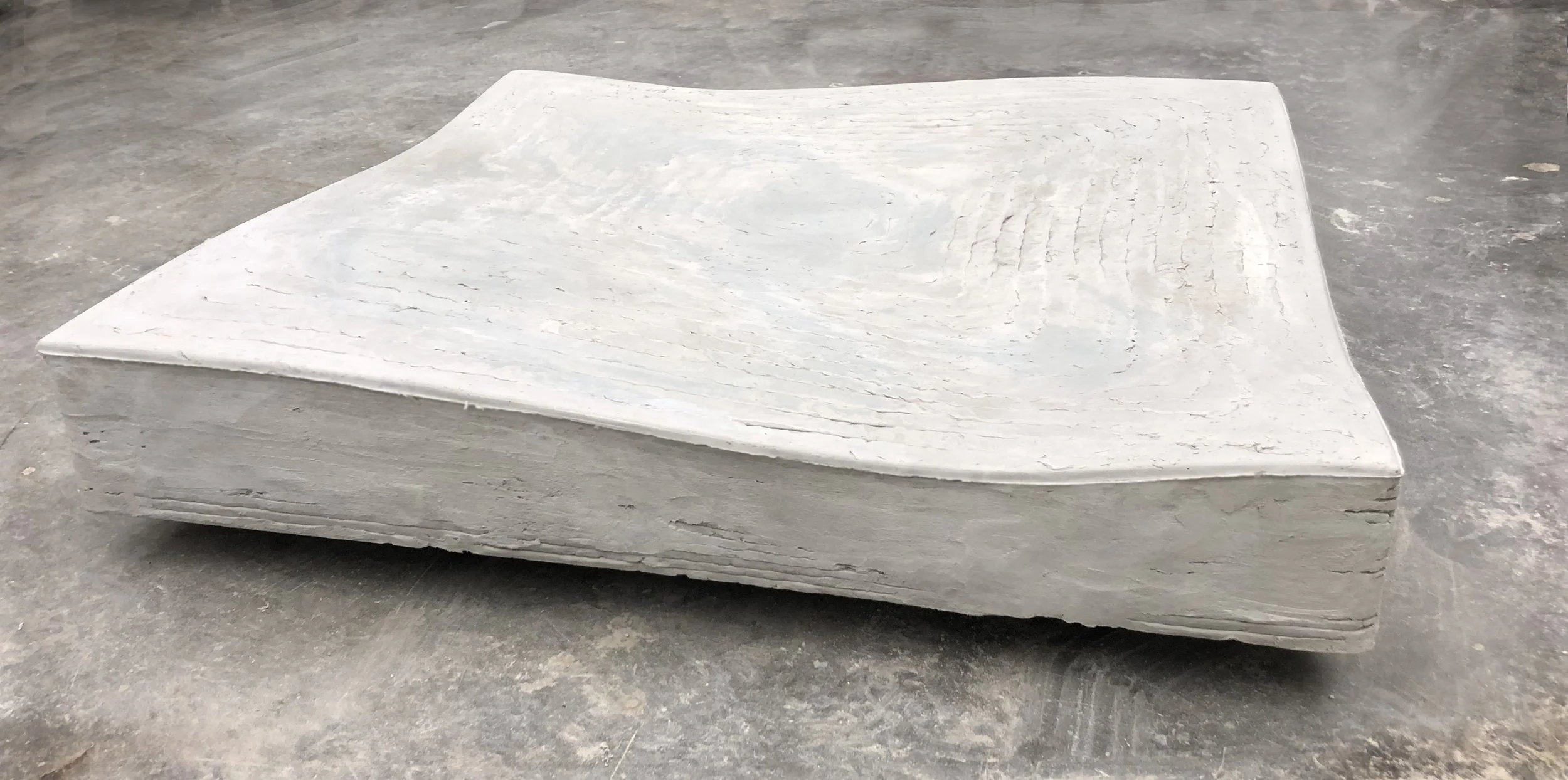



in collaboration with Wes McGee and Victor C. Li
2017-present
Additive manufacturing (AM), more commonly referred to as 3D printing, has attracted significant commercial interest due to its potential to reduce time, labor, and material use, while improving safety and overall building performance through computational optimization. The most promising application for the construction industry centers on concrete, where a significant portion of the construction cost is attributed to formwork production, which in the case of complex surface geometries or topologies can often be cost prohibitive. 3D printing concrete holds the promise of partially or completely eliminating the need for molds. Simultaneously, the design of advanced materials such as engineered cementitious composites (ECC), can be calibrated to optimize performance requirements of strength and ductility while reducing environmental impacts through a reduction in cement use. This research focuses on the development of novel approaches for concrete 3DP with ECC to rethink the design and fabrication of building envelope systems and building components. The prototypes produced include a series of columns and panels with complex geometries aided by bead shaping as well as variable layer thickness control.
Through an integrated approach to matrix/reinforcement tuning, process control, tooling and extrusion bead shaping, and computationally driven fabrication systems, the project explores the design and material constraints of 3DP ECC at full-scale.
Post-doc research fellows
Yi Bao, Duo Zhang, Kequan Yu, He Zhu
Lab Support
Asa Peller, Carlos Pompeo, Rachel Henry, Jacob Pyles
This work generously supported through the Prototyping Tomorrow Grant Initiative from Taubman College of Architecture and Urban Planning, University of Michigan, as well as an AIA Upjohn Research Grant Initiative.